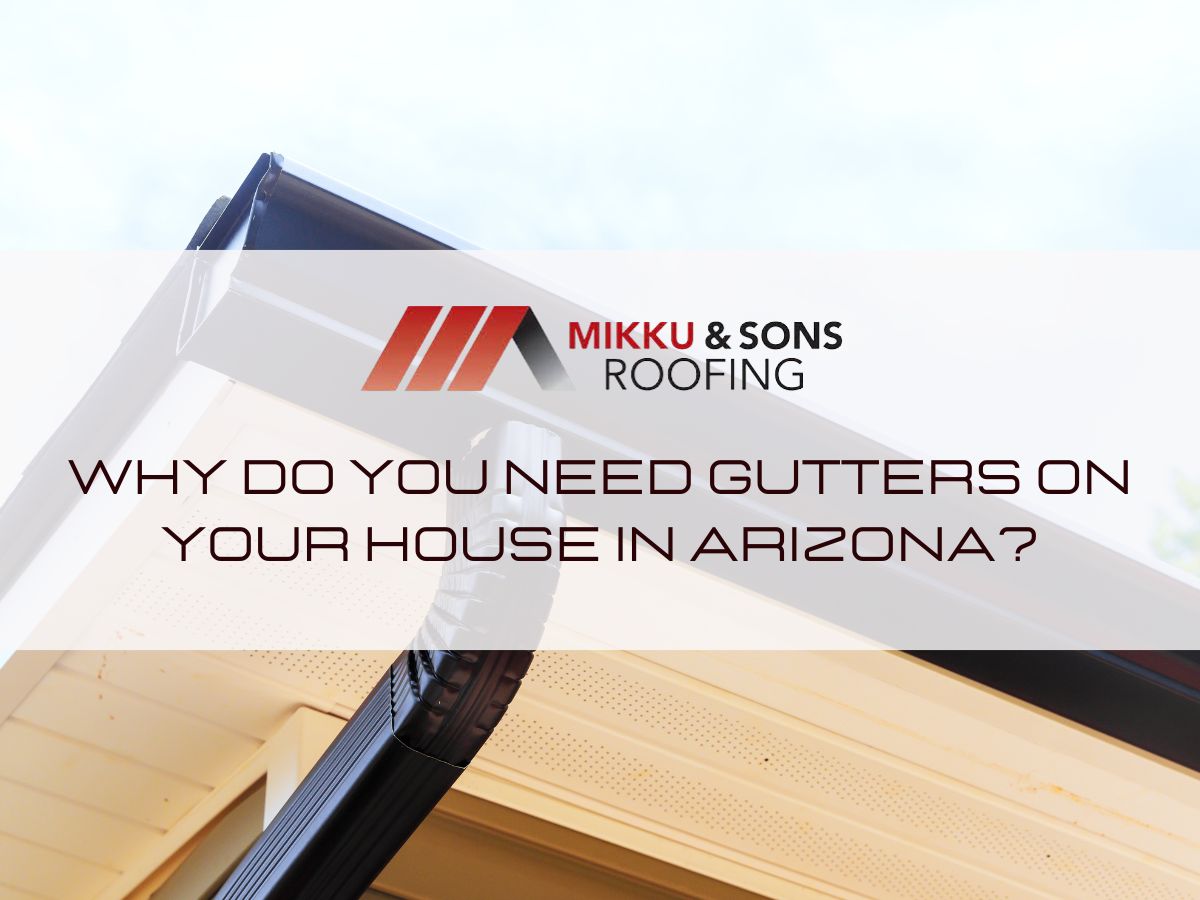
Usually, a polyurethane foam roof costs about equal to a Built-Up Roof (BUR) with underlying insulation. However, foam roofs are unique because they are the only roof type that both insulates and protects against leaks with a single monolithic barrier.
There are a lot of flat roofing materials, but all are not equal in quality. An EPDM (rubber roof) or single-ply roof, sealed either by tars or adhesives are not as high quality as a typical BUR roof.
The reason is they usually last less than 10 years, while a higher quality BUR roof may last a lot more than 10 years. Usually, a BUR roof is built with a few semi-flexible membrane layers, and then water-proofed with water-resistant modified bitumen.
Remember, coal tars are a known carcinogen (not as severe as asbestos – otherwise, this would be more widely known). Modified bitumen, however, comes from oils, refined at much lower temperatures than coal tar, and is a much safer substance.
The fluctuating prices in the cost of a barrel of oil get passed on to the roofing industry. As the costs of asphalt roofing materials continue to increase, and the cost of a high-quality polyurethane foam roof remains more steady, that makes SPF or foam roofing more affordable for consumers.
Cost, of course, can vary due to a lot of factors, like geographic location, and the size and type of the project. Prices might be estimated anywhere between $3-$12 per square foot, and this can be affected by several other factors – the quality of the materials used, the labor costs to install these materials, and any associated warranty, contractor insurance, or bonding costs which will get passed on to the customer.
If you’re going to install a roof, it’s good to think about the long-term cost impact. If you have decided to install a foam roof, the insulation factor can pay off big in the long run.
Also, think about adding cool roof coatings; just by changing the color of a roof to something reflective can lower summer cooling bills by 30% or more.
Medium Density Sprayed Polyurethane Foam Roofing conforms to the corners and angles of a roof and usually has an R-Value around 6 to 8 per inch of thickness. In layman’s terms, one inch of foam is as effective as 6 to 8 inches of solid wood.
In reality, due to things like vapor trapping (foam forms a barrier), and the density of foam (it is light, but heavier than air–of course), foam can be 4 times more effective than fiberglass.
If you have lived in an older, poorly insulated home, you know that heating and cooling bills can really get out of control with poor insulation.
This is just one final cost factor that should be considered when you’re comparing an insulated roof like SPF with other roofing materials, like EPDM, Single Ply, or BUR, with no insulation. Watch out for the myths of foam roofs.